Scuderia AlphaTauri Cranks Up Racecar Efficiency with Epicor
Formula One racing team puts an ERP solution to work to help manage production and trackside parts replacement.
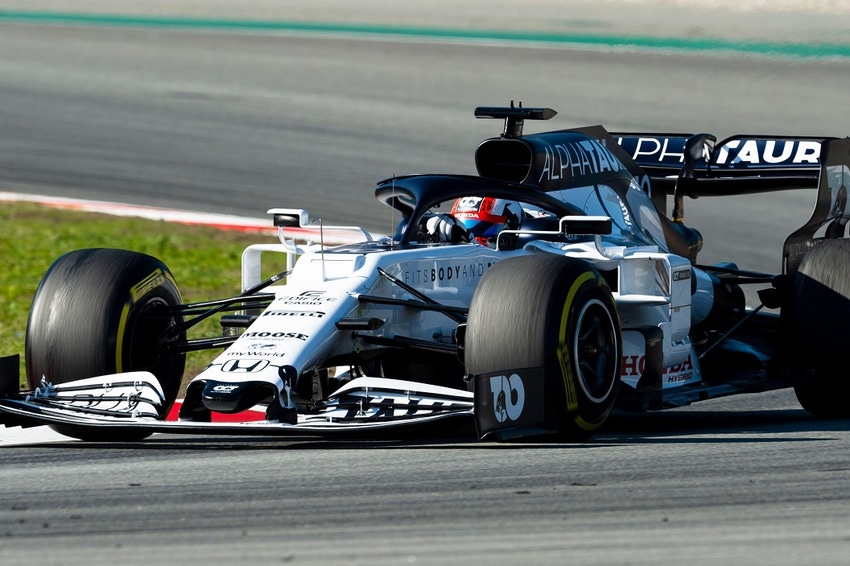
When Scuderia AlphaTauri, a Formula One (F1) team from Italy, wanted to ratchet up its efficiency servicing and maintaining its latest racecar, they turned to Epicor’s Kinetic enterprise resource planning (ERP) platform. (Kinetic is available in a cloud-based form but the racing team is not using that version.) It was a tall order, given that F1 racecars can have upwards of 14,000 parts that must be tracked and monitored. Some of the unique components may need to be custom-manufactured by Scuderia AlphaTauri.
Giovanni Cattarina, ERP manager for Scuderia AlphaTauri, says the move helped improve management of those parts and resources that go into being track-ready and beyond. The 2022 F1 racing season kicked off with Round One in mid-March and races will continue into November on tracks around the world. Cattarina says using Epicor helps the team focus their time and energy on the fast-moving operation.
How ERP Helps Scuderia AlphaTauri Go Faster
“Formula One is a business that is very dynamic,” he says. “There are many things that are going on and changing internally and externally. That’s why our technical partnership [with Epicor] is quite important for us.”
The Scuderia AlphaTauri team must manage a lot of information in a short period of time, Cattarina says, and the flexibility of Epicor helps with this. For example, prior to using the solution, he says, many individuals on the team would spend much of their time, even half of the day, entering data. Now such time can be prioritized to allow those team members to focus on other needed tasks. Data entry that might take up half a day could get done in half an hour through the solution. “Epicor helps us very much, especially in production,” Cattarina says.
There is a driving need among F1 teams to be more efficient and work lean in order to deliver on race day, says Stu Millward, vice president of professional services for Europe, Middle East, and Africa, and Asia-Pacific for Epicor. “Every hour that they spend doing something that isn’t a value-add to make the car, the parts they’re working on more efficient, resolving problems, making sure everything is optimized -- every minute, every hour they spend doing something else means that efficiency is lost.”
Operating without Epicor was a challenge, Cattarina says, for people who collected information for departments. “Prior to using Epicor, many people were using different spreadsheets,” he says. “For some departments, it was tough to even know what to do in their daily work.”
Now with the solution in place, information is available to the right personnel at the right moment, he says. “As soon as the production department completes their work, the following department knows they can start,” says Cattarina. “Information goes smoothly from one department to another, and nobody needs to collect the data. They have everything on the tablet to start.”
Supply Chain Problems, Solved Trackside
If the Scuderia AlphaTauri team discovers an issue with a car part while trackside, he says, they can use Epicor to help sort out the root cause. This can include finding out what raw materials were used and who was the supplier. Such information can also be used to improve procedures or training to avoid such problems, Cattarina says.
“Each part of the car has its own service that must be done at certain kilometer intervals,” he says. The nose box, for instance, must be checked every 200 kilometers and proof-tested. The front wing can run on the car a maximum of 2,000 kilometers. Epicor can monitor if a part is running close to an interval for replacement, Cattarina says.
The hurried pace of running a high-profile F1 team in a safe, coordinated way means efficient management of resources is essential, especially at the beginning of the season after building up a brand-new car during winter, with limited stock to replace parts. “Epicor is very important from a reliability point of view because if we miss a service on a part,” he says, “we risk that the car must stop or gets crashed at some point.”
About the Author(s)
You May Also Like