Proof Of Concept | Beyond Connectivity, Internet of Things (IoT), Artificial Intelligence (AI), 5G, Data management, Data analytics, Edge computing
Automotive lessons in 5G-enabled manufacturing have wide application
Ford Motor Company, Vodafone Business, TM Forum, and other partners are demonstrating how 5G can improve automotive manufacturing and operations in a Catalyst project, 5G enhanced manufacturing.
17 Sep 2021
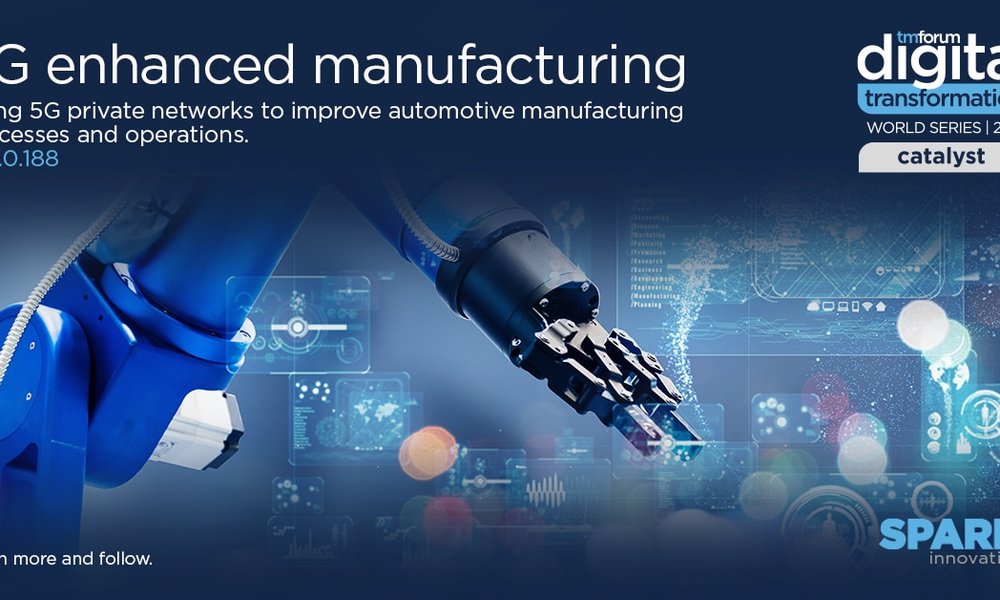
Automotive lessons in 5G-enabled manufacturing have wide application
Ford Motor Company, Vodafone Business, TM Forum, and other partners are demonstrating how 5G can improve automotive manufacturing and operations in a Catalyst project, 5G enhanced manufacturing.
The Catalyst proof of concept will showcase demonstrations from the 5G Enabled Manufacturing (5GEM) project. It was set up in June 2020 to explore use cases for 5G private networks in different manufacturing environments, exploiting 5G attributes such as superior connectivity, reduced latency and security, as well as complementary technologies such as network slicing, edge computing and AI, to process near real-time data from sensors across a plant.
5GEM is a consortium of eight organizations – ATS Global, Ford Motor Co., HSSMI, Lancaster University, TM Forum, TWI, Vacuum Furnace Engineering, and Vodafone Business – and is supported by the UK government’s 5G Testbeds and Trials Programme.
Critical manufacturing processes
Critical automotive manufacturing processes, like robotic welding of components for electric cars, require detailed monitoring and quick configuration changes to optimize the quality of the finished products. By analyzing data in real time, from 5G-enabled sensors installed across the factory, auto manufacturer Ford Motor Co. can monitor the production process and make rapid adjustments automatically in response to changes in environment, input materials and other factors.
The 5GEM team has implemented real-time process analysis and control of machines on a Ford factory floor in Dunton in the UK, investigating the advantages of connecting sensors via a Vodafone 5G Mobile Private Network (MPN) installed in the factory, including low latency, high throughput, enhanced security, and continuous remote connectivity with welding experts at TWI in Cambridge, which is also running a Vodafone MPN.
The network is also integrated with a cloud computing environment where the data is stored, processed and shared with other consortium partners in the project.
Big opportunity
The digitalization of industries provides a big opportunity for communications service providers (CSPs) and suppliers in telecoms to monetize 5G and build new revenue streams beyond connectivity. Proving new use cases and applications is foundational to this succeeding as it demonstrates the business case for investment.
Chris White, Ford’s 5GEM Project Lead, comments, “Connecting today’s shop floor requires significant time and investment. Factories are incorporating ever more autonomous equipment which cannot be hard wired because it will be moved around. Present technology can be the limiting factor in reconfiguring and deploying next-gen manufacturing systems. 5G presents the opportunity to transform the speed of launch and flexibility of present manufacturing facilities, moving us towards tomorrow’s plants connected to remote expert support and artificial intelligence.”
Changing machine configuration in production
The Catalyst demonstrates three 5G-enabled applications for automotive manufacturing. The first is changing machine configurations on the production line in real time in response to changes in the environment, which is monitored and measured by sensors connected via the Vodafone MPN.
The monitored process is laser welding for hairpin joining and battery busbar joining. High data throughput is critical because, for example, Ford will check 192 welds per part at least three times per cycle, and hundreds of welds are carried out per second, which produces large volumes of data. If conditions change, Ford needs to be able to alter machine settings within milliseconds and understand the impact on other machinery.
Standards
Equipment manufacturers need standards so that equipment can be designed to be plug and play across the automotive and adjacent sectors. TM Forum is leading the standards work in 5GEM and the Catalyst shows the Forum’s IoT standards and Open APIs in action.
Standards ensure the 5GEM solutions can be deployed in factories worldwide, even when Ford is working with different partners and suppliers. For example, 5GEM is using TM Forum’s Common Data Model and the ‘Things’ API to ensure that the solution can be easily adopted by different plants and regions.
Predictive maintenance prevents downtime
Second, automobile manufacturing processes involve many expensive machines with complicated maintenance schedules. Predictive maintenance uses data from sensors attached to machinery, together with AI algorithms deployed on edge-compute devices, to raise alerts when machines need servicing, thereby reducing downtime by avoiding breakdowns and unnecessary maintenance. This use case requires secure, high-throughput connections to access large quantities of data from the machines on the factory floor.
Remote maintenance
The third application demonstrated in the Catalyst is the remote maintenance of factory equipment using real-time augmented and virtual reality (AR/VR) to diagnose and fix problems quickly and minimize downtime. An engineer can wear a 5G connected AR headset to receive support from an expert anywhere in the world, just as if the expert was working right there in the factory. This is much cheaper and quicker than sending the expert on-site.
Watch this video of the Catalyst team talking about its achievements.
The Catalyst proof of concept will showcase demonstrations from the 5G Enabled Manufacturing (5GEM) project. It was set up in June 2020 to explore use cases for 5G private networks in different manufacturing environments, exploiting 5G attributes such as superior connectivity, reduced latency and security, as well as complementary technologies such as network slicing, edge computing and AI, to process near real-time data from sensors across a plant.
5GEM is a consortium of eight organizations – ATS Global, Ford Motor Co., HSSMI, Lancaster University, TM Forum, TWI, Vacuum Furnace Engineering, and Vodafone Business – and is supported by the UK government’s 5G Testbeds and Trials Programme.
Critical manufacturing processes
Critical automotive manufacturing processes, like robotic welding of components for electric cars, require detailed monitoring and quick configuration changes to optimize the quality of the finished products. By analyzing data in real time, from 5G-enabled sensors installed across the factory, auto manufacturer Ford Motor Co. can monitor the production process and make rapid adjustments automatically in response to changes in environment, input materials and other factors.
The 5GEM team has implemented real-time process analysis and control of machines on a Ford factory floor in Dunton in the UK, investigating the advantages of connecting sensors via a Vodafone 5G Mobile Private Network (MPN) installed in the factory, including low latency, high throughput, enhanced security, and continuous remote connectivity with welding experts at TWI in Cambridge, which is also running a Vodafone MPN.
The network is also integrated with a cloud computing environment where the data is stored, processed and shared with other consortium partners in the project.
Big opportunity
The digitalization of industries provides a big opportunity for communications service providers (CSPs) and suppliers in telecoms to monetize 5G and build new revenue streams beyond connectivity. Proving new use cases and applications is foundational to this succeeding as it demonstrates the business case for investment.
Chris White, Ford’s 5GEM Project Lead, comments, “Connecting today’s shop floor requires significant time and investment. Factories are incorporating ever more autonomous equipment which cannot be hard wired because it will be moved around. Present technology can be the limiting factor in reconfiguring and deploying next-gen manufacturing systems. 5G presents the opportunity to transform the speed of launch and flexibility of present manufacturing facilities, moving us towards tomorrow’s plants connected to remote expert support and artificial intelligence.”
Changing machine configuration in production
The Catalyst demonstrates three 5G-enabled applications for automotive manufacturing. The first is changing machine configurations on the production line in real time in response to changes in the environment, which is monitored and measured by sensors connected via the Vodafone MPN.
The monitored process is laser welding for hairpin joining and battery busbar joining. High data throughput is critical because, for example, Ford will check 192 welds per part at least three times per cycle, and hundreds of welds are carried out per second, which produces large volumes of data. If conditions change, Ford needs to be able to alter machine settings within milliseconds and understand the impact on other machinery.
Standards
Equipment manufacturers need standards so that equipment can be designed to be plug and play across the automotive and adjacent sectors. TM Forum is leading the standards work in 5GEM and the Catalyst shows the Forum’s IoT standards and Open APIs in action.
Standards ensure the 5GEM solutions can be deployed in factories worldwide, even when Ford is working with different partners and suppliers. For example, 5GEM is using TM Forum’s Common Data Model and the ‘Things’ API to ensure that the solution can be easily adopted by different plants and regions.
Predictive maintenance prevents downtime
Second, automobile manufacturing processes involve many expensive machines with complicated maintenance schedules. Predictive maintenance uses data from sensors attached to machinery, together with AI algorithms deployed on edge-compute devices, to raise alerts when machines need servicing, thereby reducing downtime by avoiding breakdowns and unnecessary maintenance. This use case requires secure, high-throughput connections to access large quantities of data from the machines on the factory floor.
Remote maintenance
The third application demonstrated in the Catalyst is the remote maintenance of factory equipment using real-time augmented and virtual reality (AR/VR) to diagnose and fix problems quickly and minimize downtime. An engineer can wear a 5G connected AR headset to receive support from an expert anywhere in the world, just as if the expert was working right there in the factory. This is much cheaper and quicker than sending the expert on-site.
Watch this video of the Catalyst team talking about its achievements.