Take a look at how manufacturers can utilize predictive asset maintenance to reduce supply chain impacts.
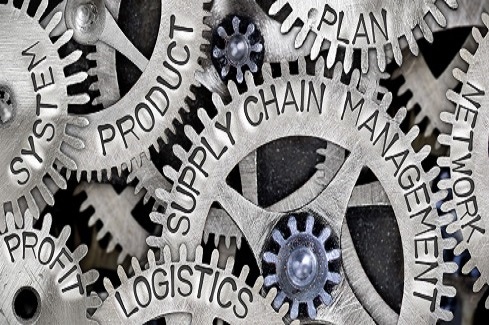
In a US survey, 8 in 10 manufacturing leaders recently said that supply chain disruptions were their primary challenge in the third quarter of 2022, and one in 10 believe these issues will improve by year-end. Inflation, COVID-19, the war in Ukraine, and Russian sanctions have further stressed supply chains.
This perfect storm of events has impacted global material shipments, resulting in excess capacity in some areas and near zero in others. In this environment, the effective use of technology can ease disruptions, improve asset optimization, enhance worker safety, and reduce risk.
Predictive asset maintenance (PAM) has delivered impressive gains over the past two decades. Manufacturers use sensors, analytics and automated processes to identify early indicators of potential issues where equipment is not at peak performance. This allows for proactive maintenance to avoid equipment failures. By deploying these advanced solutions, manufacturers can decrease maintenance costs and production downtime. It stands to reason that the market for PAM technology is slated to grow from $6 billion to $32 billion over the next 10 years.
So, how can PAM help mitigate supply chain challenges and extend the life of your current assets? When combined with new sensing and modelling technologies, PAM can do the following:
Avoid unplanned downtime: Manufacturers need equipment to process production loads when raw materials arrive. Sensors track key indicators, such as vibration or temperature anomalies while computer vision can monitor the quality of the product flowing through the manufacturing process. The integrated PAM system automatically alerts operators when sensor data falls outside of defined specifications or safety protocols. The ability to proactively identify and mitigate issues before they become major repairs or failures helps to extend the life of the asset and throughput
Automatically route production loads: Smart sensors provide operators with critical data on equipment status and digital twins simulate production alternatives. PAM technology can route production loads to different machines if issues arise. Manufacturers can achieve production goals and take other key actions, such as purchasing replacement parts to minimize downtime and slowdowns.
Optimize asset performance: Proactively servicing equipment assets can extend their lifespan significantly. This capability enables manufacturers to reduce CapEx investments and plan strategically for equipment replacements.
Improve worker safety: Equipment issues can create hazardous conditions, resulting in worker injuries. In the US, being struck by an object or equipment accounted for 9.7% of workplace incidents across all industries, whereas being compressed by running equipment or machines caused 3.7% of all accidents. Better to proactively detect and address issues before they harm workers.
Prevent latency issues: PAM requires the real-time processing of large data volumes to inform artificial intelligence models. Collecting sensor data from machinery, sending it over the cloud for analysis and returning analytics for action creates latency. By using edge technology, which computes information at or near the user and or the data source, manufacturers can gain real-time reporting on equipment exceptions. Even an incremental time advantage on issues can help manufacturers make crucial decisions, such as rerouting loads, taking equipment offline and scheduling immediate asset inspections and repairs, minimizing production impacts.
How to Push PAM to the Next Level
Some organizations may need help overcoming the limitations of legacy technology, while others will be ready to enable new use cases. Here’s how to reap value from PAM:
Develop a business case: Manufacturers should conduct an assessment to determine data and equipment readiness for PAM, as well as their budget for the initiative. Many will choose to work with a partner to speed this process, gain fresh insights and incorporate leading practices. The joint team will develop a business case that explores how to leverage new technology, like edge computing and digital twins, to gain new efficiencies. A roadmap should be crafted to deliver early and ongoing value, build internal capabilities and tackle new use cases when the time is right.
Prepare to execute: Organizations will want to collect sensor data from key assets and calibrate it with their manufacturing line to make sure assets are operating optimally. If manufacturers have older equipment that is difficult to update with digital sensors, they may want to prioritize new capital investments to digitize key processes. The best place to start is in a high-performing region at the divisional level. Key learnings from a local deployment can then be scaled.
Conduct an architectural review: The IT team will conduct a review of the current IT architecture and design the state needed to achieve PAM goals. This process involves executing assessments and interviews to understand the current level of technology maturity and what changes need to happen at a divisional, regional and enterprise level.
Deliver the solution(s): Partners can implement new technology, algorithms, and monitoring solutions. Manufacturers will gain self-healing code that can learn from big data, solve problems, and build on itself. Organizations can monitor and measure results and adjust solutions to deliver more value.
Extend the Value of PAM Solutions
Supply chain issues are stressing manufacturers, systems, and production processes like never before. Manufacturers with legacy assets will likely want to update equipment and adopt PAM to improve asset performance and reduce downtime, especially in a time of rising interest rates raising costs for capital expenditures not fully budgeted for. Those that have already adopted PAM can extend these solutions to achieve new gains, such as routing production loads to drive throughput.
About the Author(s)
You May Also Like